Column Packing
There are many types of packing on the market, each providing certain advantages for factors such as separation efficiency, capacity, fouling, and more.
Trays
Trays are simple, effective, and rugged, but limited in separation efficiency and capacity. They scale well to large diameters, heights, and multiple inputs and outputs. Many can resist fouling and operate in high stress conditions.
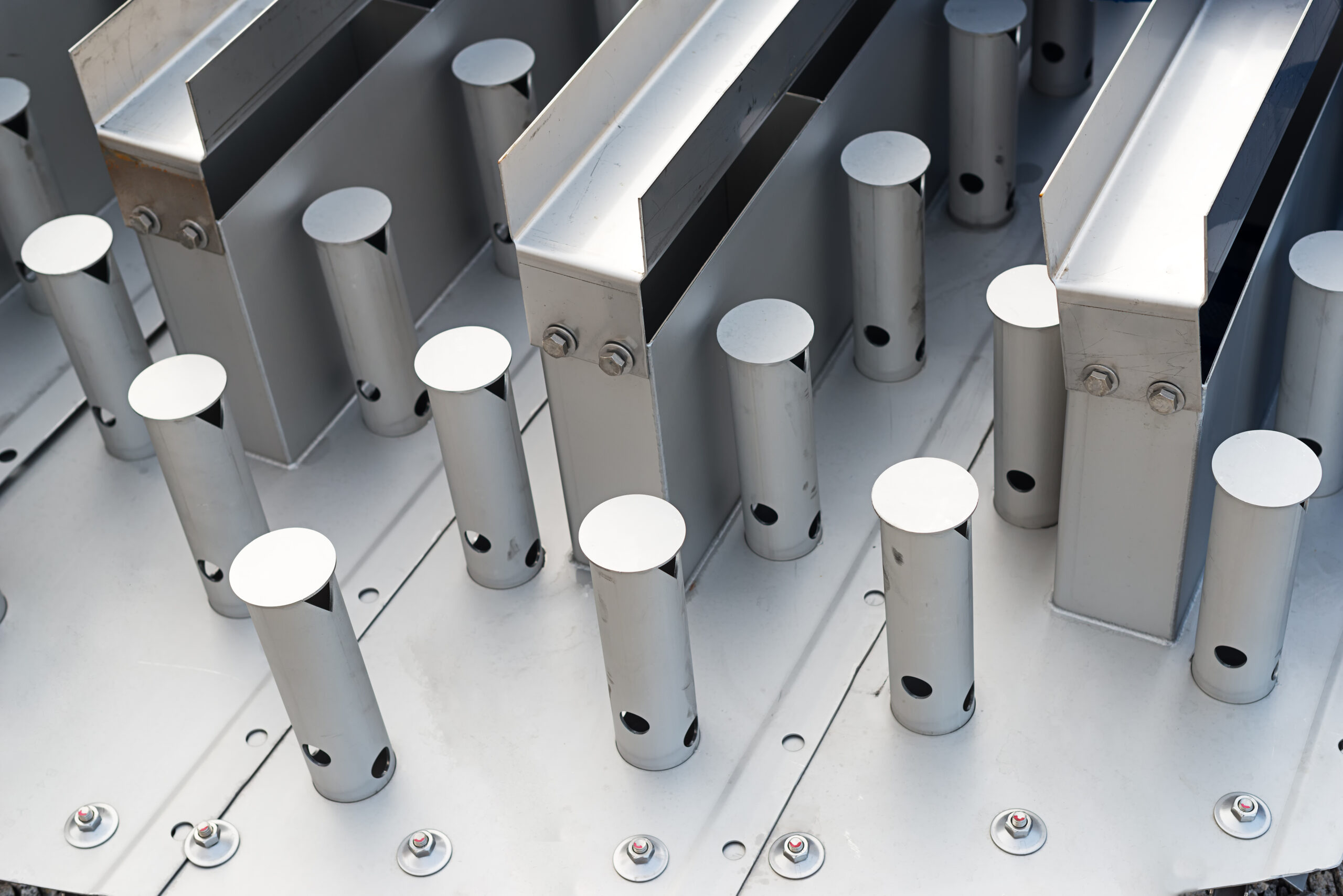
Random Packing
Random packing provides greater separation and lower pressure drop than trays, but not as much as structured packing and can be limited in scalability. It is often less sensitive to maldistribution and easy to produce from alternative materials.
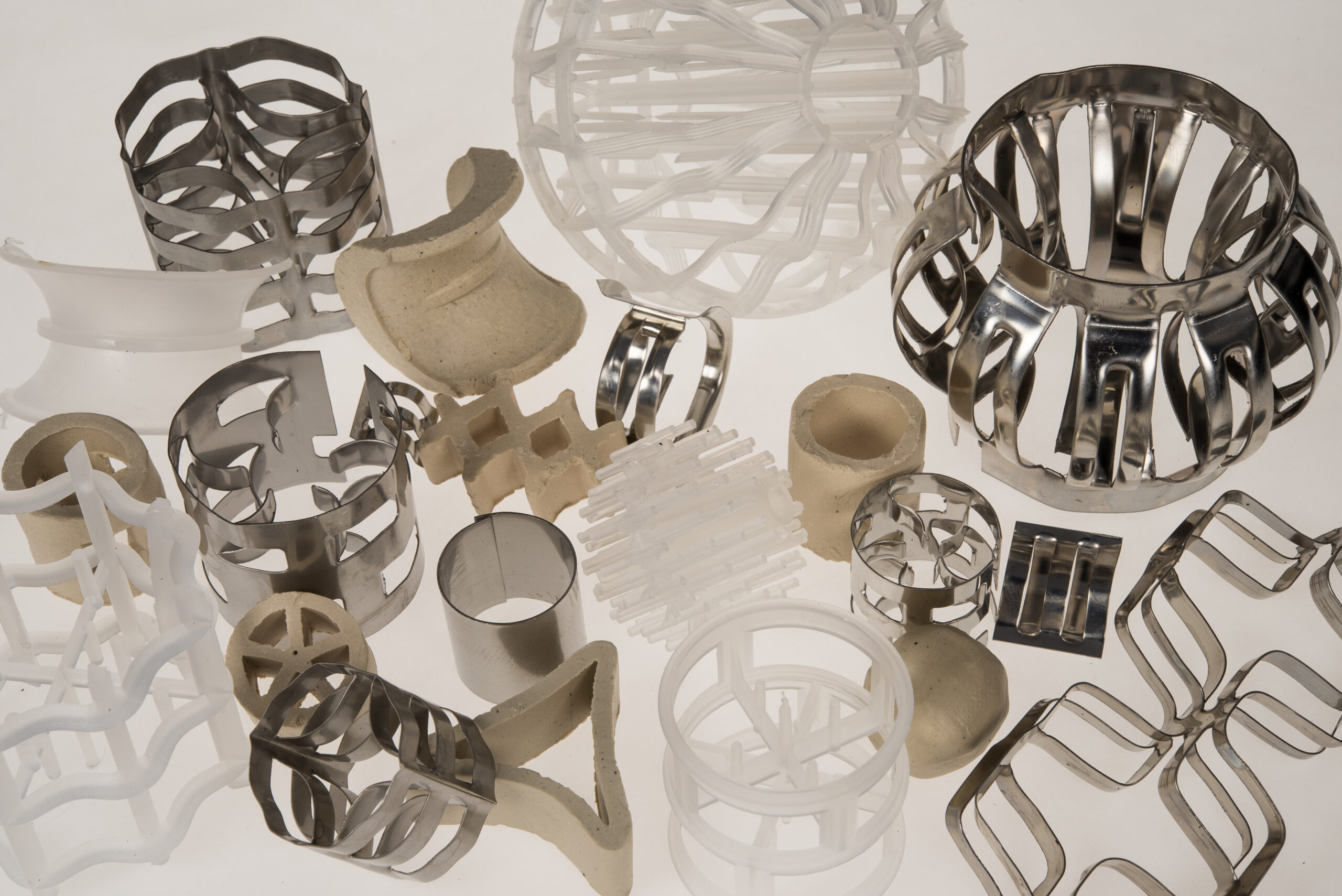
Structured Packing
Structured packing offers both high and low performance options with very good capacity and vacuum performance. It can be engineered to suit different applications. Similar to Trays, structured packing can be preinstalled and transports well, but often has high costs of implantation and can be sensitive to maldistribution and fouling.
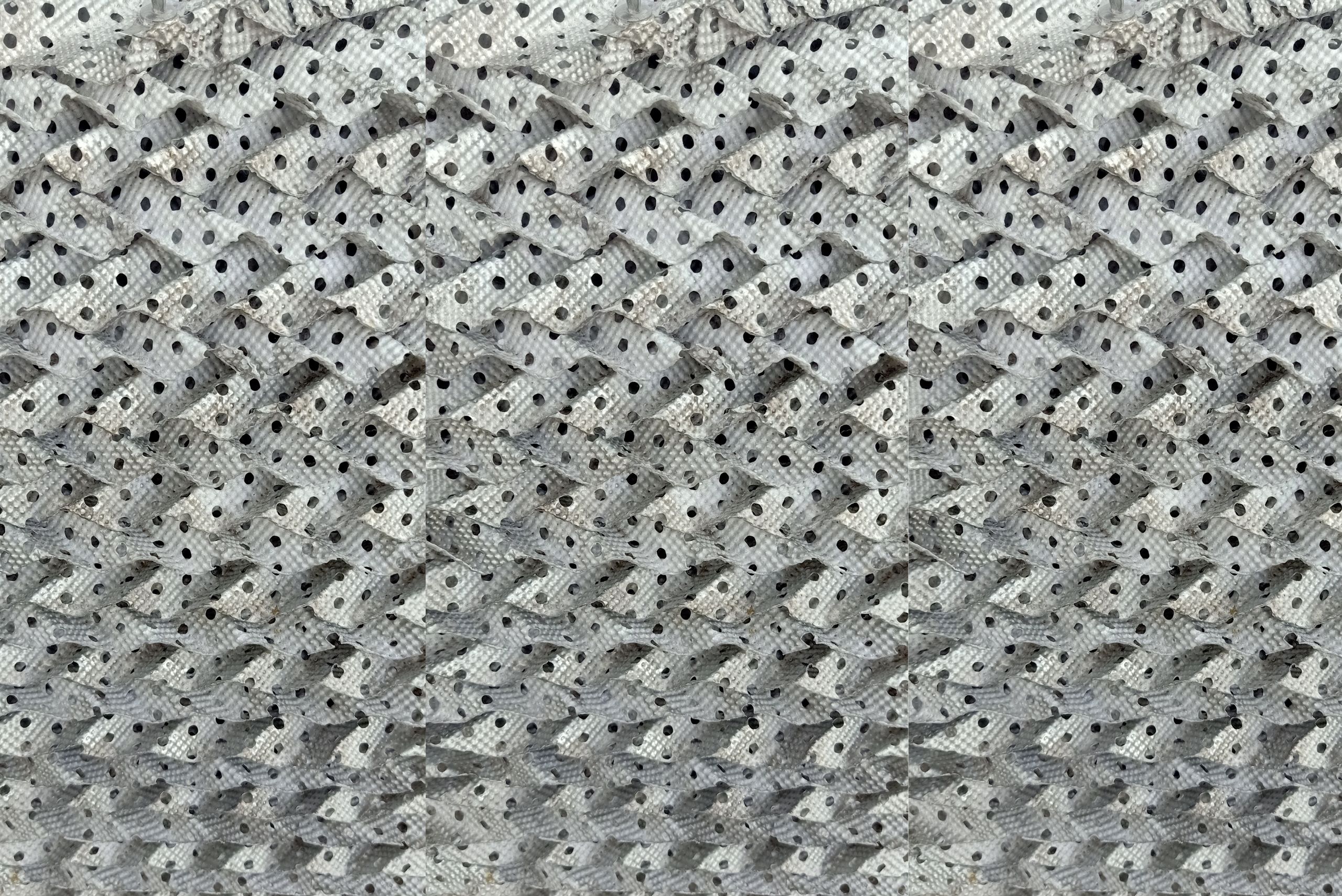
Pro-Pak®
Pro-Pak is a specialized small-form random column packing with unique characteristics that provide performance similar to high efficiency structured packing, but with the form and benefit of random packing. The special surface creates open mesh that not only offers greater free space and reduced pressure drop for its size, but wicks liquid to provide significantly greater effective surface area. Designers benefit from these properties, sometimes allowing for radical column designs. Pro-Pak is used extensively where high purity, space saving, energy saving, and/or low loading are key design factors.
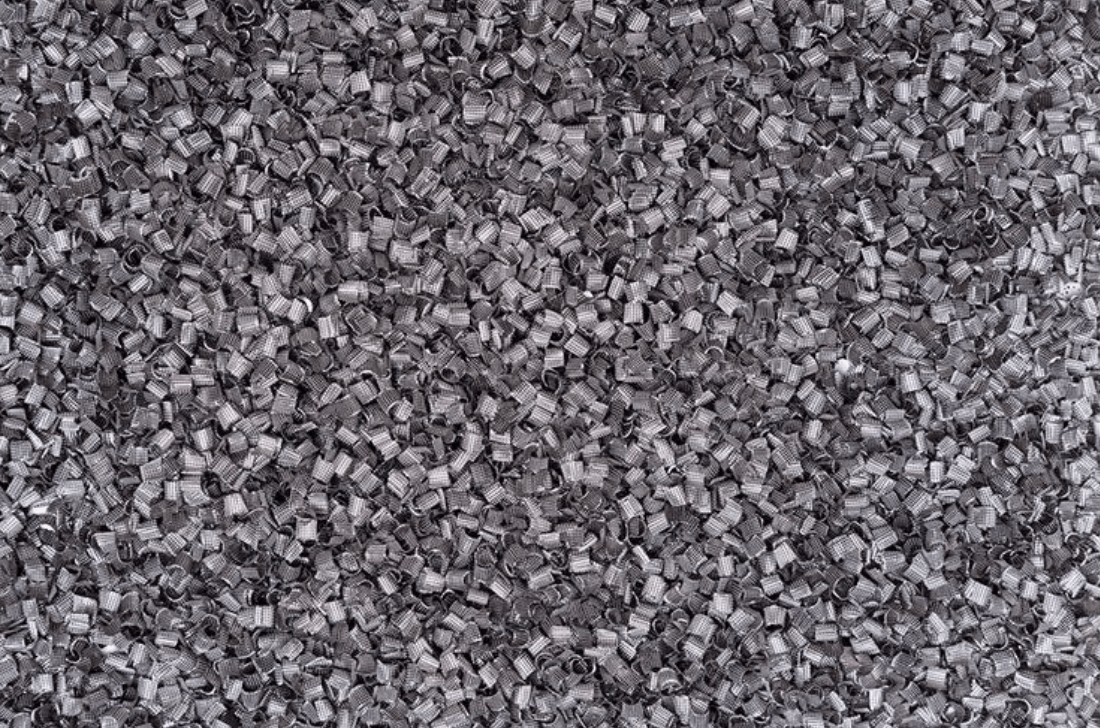
Column Internals
To operate a column efficiently, the vapor and liquid phases must be distributed evenly across the cross-sectional area of the column for the full height of the column. During operation, the pressure exerted by the rising vapor tends to push liquid towards the walls of the column. In a short column this does not severely affect results, but as columns become taller effects of maldistribution are more apparent. We provide several column internals made to mitigate the effects caused by this maldistribution.
Interdistributors
PDS produces interdistributors using an open mesh design with suspended coalescing cones. These cones create preferential liquid paths while allowing the vapor to freely travel and equilibrate across the cross sectional area. These are effective as both packing supports and phase distributors in columns with random packing. As phase distributors, interdistributors improve flow distribution when used spaced every meter inside the column, maintaining good hydraulics through the column height.
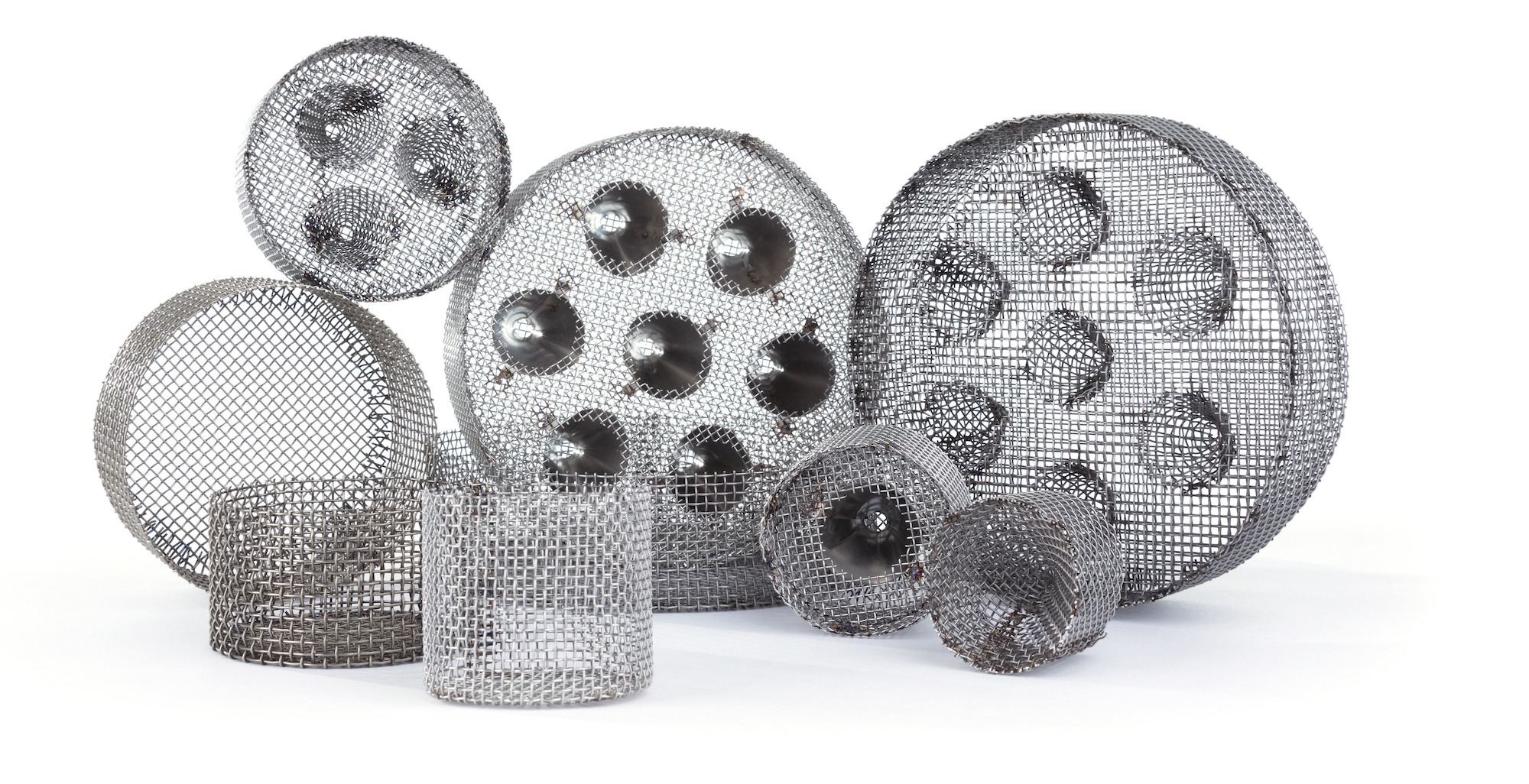
Hold Down Screens
Certain processes may introduce some instability to the packing bed. There may be bumping and foaming coming from the reboiler or flooding conditions within the column that can disturb the packed bed. In the worst case scenarios, the bed may travel outside of the column. Our hold down screens are a simple cap made of wire mesh that is held in place underneath the top flange of the column. This prevents packing loss and restrictions in your nozzles and condenser.